Often selected for garage applications, overhead doors can be used for various large openings, as well as in locations where there is limited space, for example, a wall with multiple doors side by side. When specifying these counterbalanced doors for commercial or industrial projects, the fact various products share a common outward appearance could suggest they are also quite comparable in performance.
However, similarity in form does not mean equality in function. When a certain overhead door is being selected for a specific application, it can be difficult to know which other Division 08 products meet the specifications. Gauging a door’s suitability involves considerations and comparisons for insulation, material, panel composition and other design attributes.
It is also important to know that North American garage door manufacturers are members of DASMA (Door & Access Systems Association). This association developed the standard for sectional overhead‑type doors, ANSI/DASMA 102 (American National Standard Specifications for Sectional Overhead Door Type Doors).

Need help?
When the time comes to select a commercial or industrial garage door, contact us for assistance. We can advise you in choosing the right door and can supply you with a no obligation written quotation.
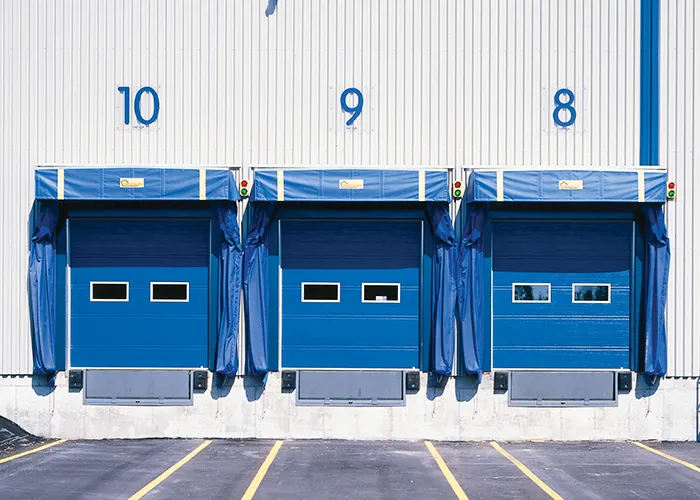
Insulation Considerations
As heating and cooling costs continue to rise, insulation value should not be sacrificed when selecting an overhead door. Although a higher R‑rating can be more expensive up front, there is a return on investment (ROI) from the potential for substantial energy savings. Some manufacturers argue a lower R‑rating can still be considered acceptable because the door is kept open to the outside elements, but with building owners paying increasing attention to energy costs, openings are more closely monitored to ensure they remain closed.
The two main types of insulation material used in the manufacturing of overhead doors are polystyrene and polyurethane. The former is less expensive and, depending on the production method, offers an R‑value between 3.5 and 5.0 per 1 inch (25.4 mm), while the latter offers an R‑value between 6 and 8. This means less polyurethane material can be used to produce the same R‑value as more polystyrene. In other words, even when two doors are of comparable thickness, the insulation properties of one could be twice that of the other.
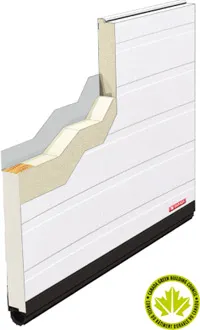
Polyurethane also offers other advantages over polystyrene, such as resistance to the petroleum‑based solvents found in many commercial and industrial applications. Additionally, the material is stable up to 120 °C (248 °F), compared to the 74 °C (165 °F) limit endured by polystyrene. When a door faces south or west, reaching a surface temperature of 74 °C (165 °F) is by no means unusual. Finally, polyurethane foam neither sags nor decomposes, offering a higher strength‑to‑weight ratio than polystyrene.
Depending on the insulation used, there are two methods of inserting the material between the two skins. With the first technique, a sheet of precut foam is placed in the middle, with an adhesive often added to affix the foam between the skins. Commonly used with polystyrene, this method has many drawbacks, such as gaps between the foam and skin, lower compressive strength and greater chance of delamination where the skin separates from the foam, further reducing panel strength.
The other option, common with polyurethane, comes at a higher up‑front cost, but its ability to provide energy efficiency can lead to a quicker payback. It involves pressure‑injecting foam between the two skins, which then fills and conforms to the contour of the panel’s inner cavity. The foam adheres to the skins, increasing their strength and reducing the chance of delamination. With this method, it is important to keep the panel under pressure to prevent the foam from expanding too far and deforming the final product. Allowing enough cure time for the foam is also necessary to ensure a quality result. This method produces a far superior panel and must not be overlooked when comparing overhead doors.
Note that there are two methods for injecting polyurethane foam into garage door sections. One is the pour‑in‑place method while the other is by continuous spray. Each method has its advantages however they yield the same results when it comes to technical performance.
Airtightness Considerations
The three main styles of joining the door panels are shiplap, tongue‑and‑groove and pinch‑resistant connections. The style specified can influence the amount of air infiltration, which has an effect upon the door system’s thermal resistance. Air infiltration should not exceed 33 ml (1.1 oz.) per second, based on a pressure of 0.075 kPa (0.01 psi) using ASTM E 283, Standard Test Method for Determining Rate of Air Leakage Through Exterior Windows, Curtain Walls, and Doors Under Specified Pressure Differences Across the Specimen. Based on this author’s feedback from the field, shiplap joints have been found to provide a lower air infiltration than tongue‑and‑groove joints, resulting in energy savings.
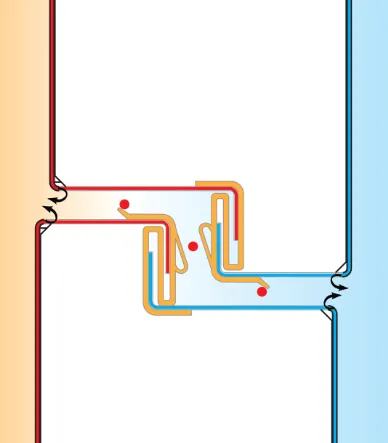
Having a properly designed thermal break in the door panel increases both thermal resistance and energy savings. To have an effective break, the front metal skin must not touch its back metal counterpart. When the skins meet along the length of the panel or at the ends via a metal end‑cap, both heat and cold transfer through conduction, resulting in lower thermal resistance and higher energy costs. During cold weather, ice buildup can be common on the inside of the panel at the metal end‑caps or between the panels of not thermally broken. This ice buildup can cause the door to malfunction and put added stress on the opener when the panels are frozen together.
Outer Skin Specifications
The thickness of the skins provides two main benefits – the strength of the door panel and its level of puncture resistance. Structural integrity is always important and not much leeway should be given when a certain skin thickness is specified. Measuring the thickness of a sheet of galvanized steel is done in gauges. On the other hand, the thickness of aluminum is measured in millimeters or in thousandths of an inch. The two main types of material used for overhead doors are steel and aluminum. Each option offers different advantages over the other, but no one material offers the best of all features.
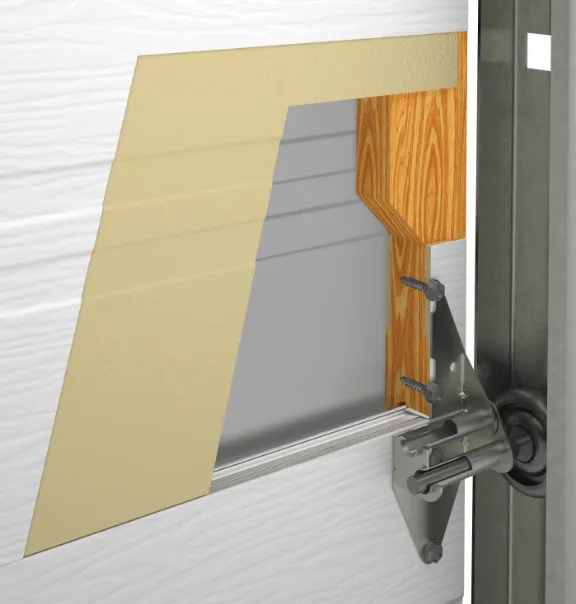
Steel
Steel is readily available in a variety of gauges and in numerous colors. It has better tensile and compressive strength than aluminum and is also less expensive. The majority of garage door manufacturers use at least 26‑gauge galvanized steel on both sides of a door. It should be remembered that the lower the gauge, the thicker the steel.
However, it is critical the steel be coated for protection against corrosion. The type and quality of this coating determines the longevity of the door panel. At minimum, it should meet ASTM International A653 and ASTM A653M, by having at least a G‑60 galvanized zinc coating (or Z‑180 or 180 g/m2). The two‑layer polyester paint finish should conform to standard ASTM A924 (A924M), and have a thickness of 0.025 mm (1 mil). DASMA has prepared a chart to assist in better understanding thicknesses of galvanized steel, bare steel and aluminum that may be used by various manufacturers.
Aluminum
When speaking of aluminum commercial garage doors, we are primarily referring to service‑station type doors or those fully glazed. Both of these types are manufactured with extruded aluminum and have different kinds of double‑paned glass. To withstand the elements, the extruded elements should be at least at least 0.06 inches (1.6 mm) thick, at least 1/8 inch (3.2 mm) thick where the hinges are attached and at least 6 ¼ inches (159 mm) thick around the perimeter of the door. If the width of the doors exceeds 14 feet (4.3 m), the aluminum extrusions should have integrated reinforcement. They should also meet the ASTM B 209 (ASTM B 209M) standards.
Frequently, the bottom section of the door is reinforced with plywood and is covered with sheet metal. This section may also be made using a panel injected with polyurethane foam like the top section. Opt for sections where the total thickness is at least 1 ½ inches (38 mm) or preferably 1 ¾ inches (45 mm).
When it comes to selecting the type of glass for these doors, there is a wide range of choices. However, ensure that the glass is double pane and sealed.
Door Panel Design
The thicker the door panel, the greater the impact strength and insulation value, depending, of course, on the type and application method of the insulating foam, as previously mentioned. Most sectional garage doors vary in thickness from 1 ½ to 1 ¾ inches (38 to 45 mm) and are injected with polyurethane foam. A thicker door panel contributes to the opening’s overall safety when combined with suitable hardware, such as tracks, hinges, rollers, struts and springs. This is the backbone for the system as it carries the weight of the door and facilitates panel movement.
In most cases, the skin of the door is not strong enough to hold the screws, lags or the operator connection. As such, reinforcements are found behind the skin and provide an anchor point. These reinforcements can be steel plates or a continuous strip of steel along the panel with wood end‑blocks, with the latter providing more material for the screw threads to hold onto. Without adequate reinforcements, the hinges or operator connection may pull apart from the skin of the door panel. When steel reinforcements are used, 14‑gauge steel should be the minimum accepted thickness for maximum holding power.
Hardware Components Design
Without proper hardware, an overhead door could fail while in operation causing damage to the door itself or objects passing underneath, as well as posing a serious threat to people in the immediate area.
In most commercial and industrial applications, 12 to 14‑gauge hardware should be the minimum specified. Springs must be properly calculated to handle the daily cycles of the door system. The number of spring cycles can vary from 10,000 to 100,000 cycles. However, you must realize that you cannot get the high cycles for every size of door. If you want the best operating system, with the highest cycles possible, specify “springs shall be designed for the maximum operation cycles”.
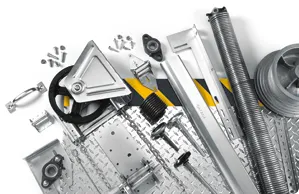
To carry the dead weight of the panels when left in the “open” position, overhead system tracks (vertical & horizontal) should be 3 inches (76 mm), and double hinges should be specified when the opening is 12 feet (3.7 m) or wider. Due to the high number of cycles and the heightened importance of the doors functioning properly, the correct choice of hardware is critical in reducing both maintenance costs and the frustration of a broken door.
Reinforcement struts should be based on both the weight and wind load expected for the application. As it is usually the largest opening in a facility, structural damage to both the door and building could occur should the overhead system fail.
Window considerations
When trying to maximize natural lighting in a building, an evaluation of the building’s level of security and its desired energy efficiency should be made in tandem. If security considerations are critical, it would be best to place windows at a height where a normal person is not able to see inside. As for energy efficiency, more windows reduce the level of insulation, hence raising energy costs.
If windows are necessary for the application, sealed double‑paned units should be favored. These windows must be at least ¾ inch (19 mm) thick and have an air space between the panes of at least ½ inches (13 mm). The panes ought to be sealed in aluminum extrusions.
There are also windows called panoramic which consist of panes set into an aluminum extrusion. These should similarly be sealed and double pane. For these two window models, it is important to specify that all components are assembled at the door manufacturer’s plant.
Conclusion
Since the warranty is a good indicator of the confidence of the manufacturer in their products, a strong pledge should never be overlooked when determining the best overhead door system for the application. This is also an area where reading the complete warranty can prevent misunderstanding in the future.
Nevertheless, using the warranty as the sole gauge of an overhead door’s performance expectations can be a mistake, it must be considered alongside the numerous other points mentioned within this text. An overhead door system must not be judged by its outward appearance. By reviewing the elements listed above, the proper door can be determined for the application. When it comes time for product selection, it is important to ensure each potential door assembly is carefully compared to ensure the specifications are not downgraded by substituting an inferior system.